Pipe Dreams: Uncovering the benefits of PVC-O Technology
In the realm of construction, the choice of materials can significantly impact the longevity and overall quality of a project. One such crucial material is pipes, which form the unseen yet vital network within buildings. PVO Pipes have emerged as a reliable and durable solution, offering a range of benefits that make them the preferred choice for builders and contractors worldwide.
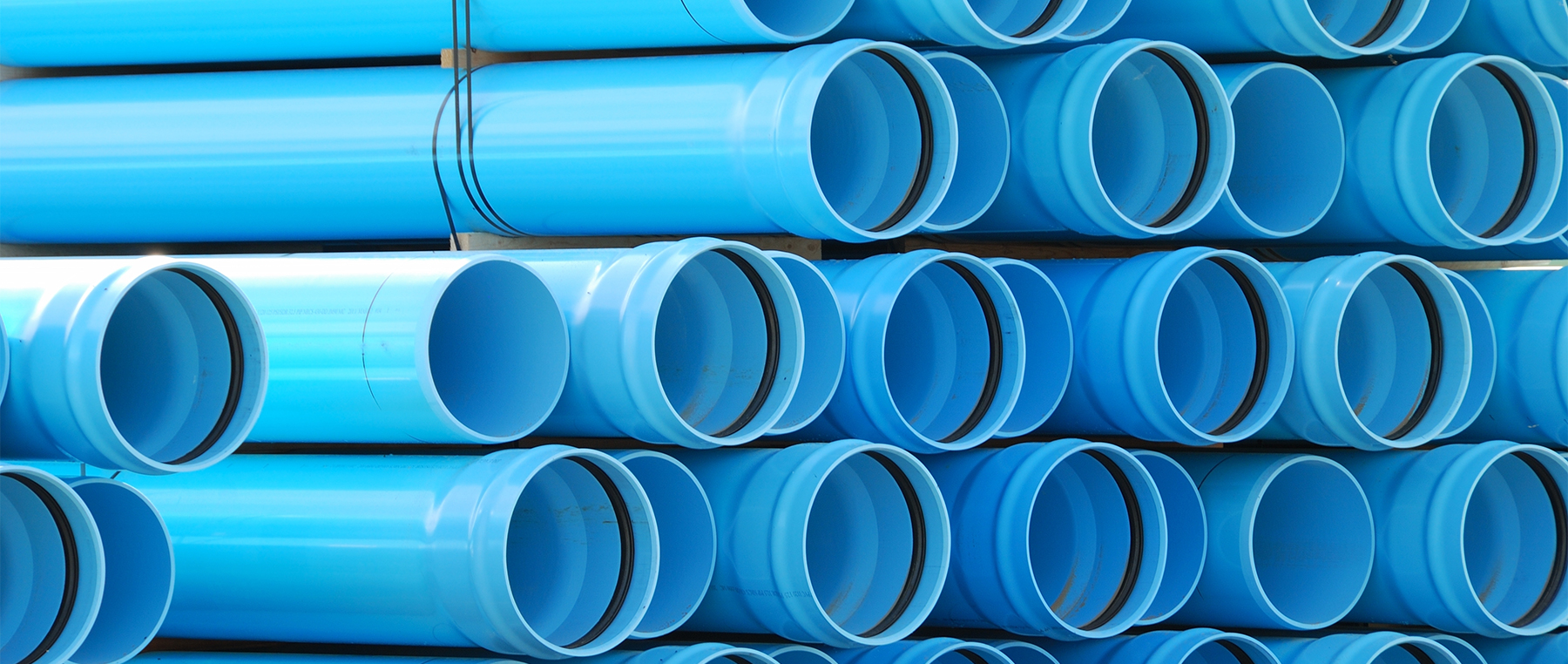
The PVO Advantage
PVO Pipes are renowned for their exceptional durability and resistance to various environmental factors. Here's why they stand out:
- Superior Strength: Engineered to withstand high pressures and heavy loads, PVO Pipes provide unmatched structural integrity.
- Corrosion Resistance: Their advanced manufacturing processes and high-quality materials ensure long-lasting performance, even in harsh conditions.
- Flexibility: PVO Pipes offer flexibility, making them ideal for complex installations and tight spaces
- Leak-Proof: Their precision manufacturing minimizes the risk of leaks, ensuring efficient and reliable fluid flow.
- Fire Resistance: PVO Pipes are designed to withstand high temperatures, providing an added layer of safety.
Applications of PVO Pipes
PVO Pipes find extensive applications in various sectors, including:
- Plumbing Systems: For efficient and reliable water supply and drainage.
- Irrigation Systems: For precise and efficient water distribution in agriculture and landscaping.
- Industrial Piping: For handling a wide range of fluids and gases in industrial processes.
- Municipal Infrastructure: For robust and long-lasting water and sewage systems.
Manufacturing Process of PCVO Pipes
PCVO (Pressure Class Vinyl-Oxide) pipes are primarily used for underground drainage systems due to their excellent resistance to corrosion and impact. Here's a general overview of their manufacturing process:
Raw Material Preparation:
- PVC Resin: This is the primary material, a thermoplastic polymer known for its durability and flexibility.
- Additives: Various additives like stabilizers, lubricants, and impact modifiers are added to enhance the pipe's properties.
Extrusion Process:
- Melting: The PVC resin and additives are melted together in an extruder.
- Shaping: The molten mixture is forced through a die, shaping it into the desired pipe profile (circular, oval, etc.).
- Cooling: The extruded pipe is cooled rapidly, solidifying its shape.
Curing Process:
- Cross-linking: The PVC molecules are cross-linked to improve the pipe's mechanical properties, such as strength and resistance to heat and chemicals. This process is often done using a peroxide catalyst and heat.
Expansion and cooling:
Preform pipes exit from the oven and are introduced into a mold where they are expanded to obtain the final PVC-O pipe with the help of Compressor Air.
Extraction:
The PVC-O pipes are withdrawn sequentially and packed for subsequent storage and shipping to customers.
Use of Compressed Air in PVC-O Pipe Mfg
Compressed air up to 35 bar is used during the Expansion Phase to blow the pipe inside a mould to obtain the required size.
The pressure of the air is kept constant and the flow rate is regulated in downstream within the equipment based on the required pipe size to be manufactured.
The temperature, flow, pressure & quality of the air is crucial for this process to be completed without any defects.
The Industry relies on ESCL’s BREEZE range of machines for this application. The BREEZE series is a Air Cooled compressor which can deliver up to 44 barg at very low discharge temperatures, maintaining a constant flow and pressure.
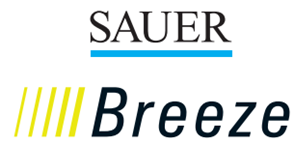
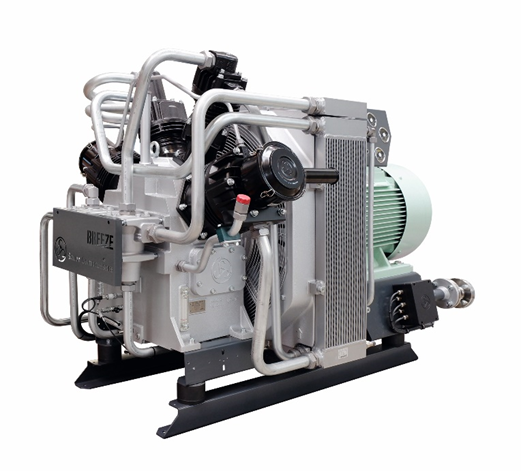
- Advanced high efficiency cooling arrangement
- Inter-stage cooling increased by 30%
- Extended capacity range from 280 to 365 m³/h
- Enhanced safety
- Advanced high efficiency cooling arrangement
- Lowest vibration due to superior mass balance
- Classical, robust design of running gear and technical layout
- Fits into every room with a minimum of interfaces
- Easy access, easy inspection and maintenance friendly design